Disaster Prevention Measures for Fuel TanksOur Company / Approach to Safety
Related Laws and Disaster Prevention Measures
Disaster prevention measures for fuel tanks installed in thermal power stations are
taken for each facility in accordance with the Fire Service Act, the Act on the Prevention of
Disasters in Petroleum Industrial Complexes and Other Petroleum Facilities, and the High Pressure
Gas Safety Act, etc.
In particular, the company is taking the following countermeasures at power stations located in
special disaster prevention areas such as petroleum industrial complexes and other petroleum
facilities, depending on the scale.
- Establishment of management systems through the appointment of a disaster prevention manager and a deputy disaster prevention manager and the creation of disaster prevention regulations
- Installation of disaster prevention equipment and materials, such as chemical fire trucks, oil recovery and oil fence vessels by the Self-Defense Disaster Prevention Organization and the Joint Disaster Prevention Organization, and deployment of disaster prevention staff necessary for this purpose
- Establishment of reporting systems and other systems for disaster prevention
Content of Measures
Thermal power stations mainly handle LNG (liquified natural gas), LPG (liquefied
petroleum gas), and heavy crude oil. The following leakage and fire prevention measures are taken
for such hazardous materials.
To prevent hazardous materials from catching fire, prevention of the occurrence of the following
three conditions is important.
The 3 Conditions for Fires/Explosions | Fire Prevention Measures |
---|---|
①Occurring in a Closed Place (Presence of Combustibles) | Installing fuel facilities outdoors and not installing them in a closed place |
②Flammable Gas Mixed with a Certain Ratio of Air (Presence of Oxygen) |
|
③Existence of an Ignition Source |
|
Even in the event of a fire, the equipment is located so that the heat and gas
generated by the fire will not affect the outside of the premises.
In addition to the use of fire-fighting equipment on the premises, disaster prevention systems,
including an in-house fire brigade stationed on the premises of the power station, public fire
departments, fire engines owned by cooperatives for disaster prevention, and disaster prevention
water vessels (for when land traffic has been cut off), etc., have been enhanced to enable swift
fire-fighting activities.
[Main Facilities for Fire Prevention and Extinguishing]
- Foam fire extinguisher
- Sprinkler water-supply facilities
- Drainage facilities
- Inert gas extinguisher
- Water curtain (LNG and LPG)
- Chemical fire extinguishing facilities
- Including chemical fire engines
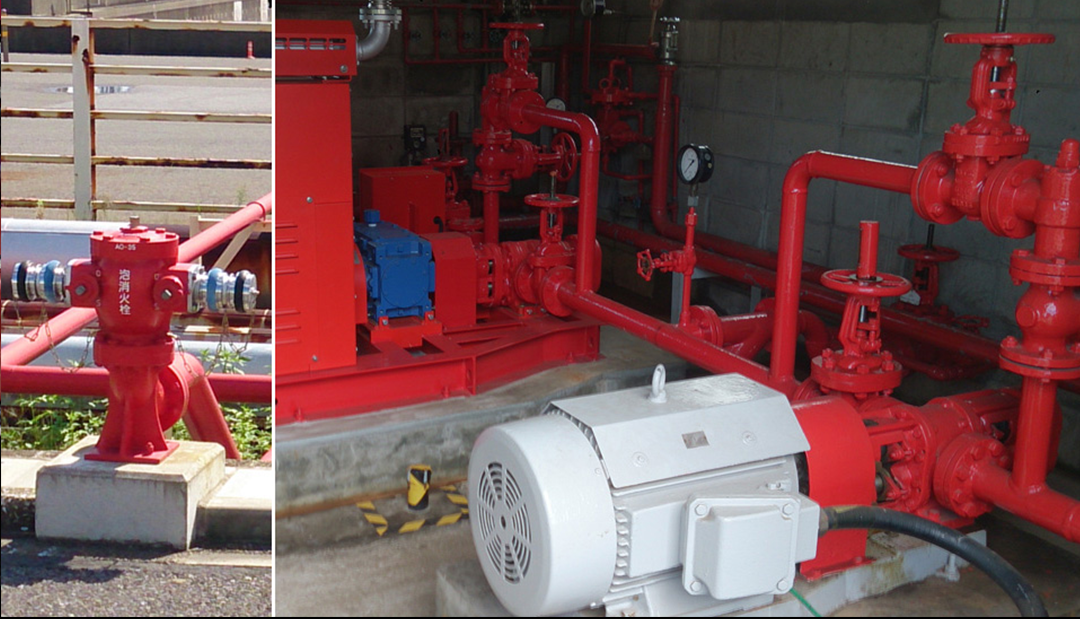
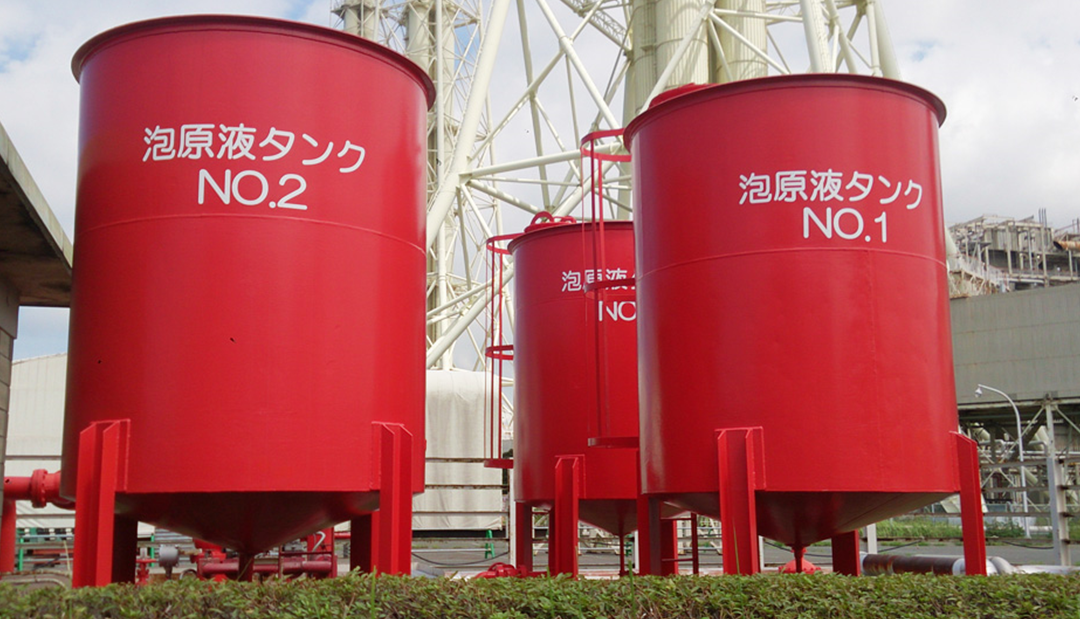