the next memory
A Relentless Commitment to Safety
2024.12.13
This three-part series takes an in-depth look at the decommissioning of Units 1 through 6 at Kashima Thermal Power Station. Part 2, divided into two installments, highlighted the plant’s contributions to Japan’s stable power supply throughout periods of economic growth and stagnation. In this final installment, we look toward the future beyond the decommissioning process.
In addition to Kashima Thermal Power Station, JERA is also planning to decommission other locations, such as Chita and Oi Thermal Power Stations. What drives these decommissioning efforts? And how does Kashima Thermal Power Station serve as a pioneering force in this journey? Here, we delve into the enduring challenges—past, present, and future.
>> Read Part 1: “Responsibilities” Fulfilled by the Top Runner >> Read the first half of Part 2: A Commitment to Stable Energy Is in Our DNA >> Read the second half of Part 2: A Commitment to Stable Energy Is in Our DNAINDEX
- Cutting-Edge Decommissioning Powered by JERA’s Expertise
- Communication—The Beating Heart of Safety
- Thoughtful Considerations for All On-Site Workers
- Building a Culture Where Everyone Is Treated as Part of the Team
- Sharing Decommissioning Expertise Across Japan
- Following Kashima’s Lead: Challenges at Chita and Oi Thermal Power Stations
Cutting-Edge Decommissioning Powered by JERA’s Expertise
JERA operates 26 thermal power plants across Japan, and its O&M and Engineering Division has accumulated extensive expertise spanning plant development, construction, operation, and maintenance. Tetsuya Watabe, Corporate Vice President, Managing Executive Officer, Director, and Chief O&M Engineering Officer (COMEO) shared his insights on the significance of decommissioning projects:
“Each power plant has its own story developed in close partnership with the local community,” Watabe says.
"Power plants operate on land that holds immense value for local residents and exist only through the community’s understanding and trust. Much like construction and operation, a plant's decommissioning is part of an ongoing process and embodies our commitment to business activities rooted in coexistence with the community."
Community development remains the top priority when considering redevelopment and land use after decommissioning. Watabe adds, “Power plants are often located in industrial zones or near residential neighborhoods. While each location serves a unique role, we firmly believe that every site should have a positive impact on the community.”
The planning for the decommissioning of Units 1–6 at Kashima Thermal Power Station started in 2015 and marks JERA's first time taking a project like this from start to completion. Guided by JERA’s mission to “provide cutting-edge solutions to the world’s energy issues,” we are pursuing new approaches that move beyond conventional thinking.
Specifically, we are adopting construction methods and waste disposal techniques that account for the environment and align with the latest industry standards. At the same time, we are committed to creating a safe and comfortable work environment for everyone on-site.
While inspecting the decommissioning site, Watabe underscores, “Safety remains the top priority in everything we do.” He reiterates this commitment during every site visit.
Watabe, who frequently visits the decommissioning site, consistently emphasizes that he wants everyone working at the plant to treat each other as part of the same team.
The decommissioning process is led by the primary contractor, with support from various partner companies. On-site personnel, including workers from our partner companies, face the highest risks. This is one reason why JERA must uphold an unwavering commitment to safety, seeing everyone on-site as part of one unified team.”
Communication—The Beating Heart of Safety
The dismantling of boiler flue ducts for Units 3 and 4 is currently underway.
August 2024 – Amidst the sweltering heat, excavators at Kashima Thermal Power Station start to dismantle the boiler flue ducts of Units 3 and 4. “We started by removing insulation materials that posed a risk of becoming airborne. Since July, we’ve moved on to the next phase: dismantling the flue ducts using heavy machinery,” explains Shinichi Kohata, Manager of the O&M Mechanical Unit at Kashima Thermal Power Station.Kohata is responsible for safety oversight, process management, budget control, and administrative tasks related to decommissioning, as well as the patrol, maintenance, and management of operational Unit 7 and other facilities.
Kohata, now in his eleventh year at Kashima, has overseen boiler construction and decommissioning at several power plants.
Decommissioning Units 1–6 at Kashima Thermal Power Station involves unique challenges, including active equipment within the decommissioning zone, requiring regular coordination for periodic inspections and maintenance.
“At Kashima Thermal Power Station, Units 1–6 are undergoing decommissioning, while Unit 7 remains operational. Dismantling Unit 3, for instance, requires careful management to avoid impacting the piping and drainage systems connected to Unit 7. We cannot proceed without ensuring these systems remain fully functional.”
Another challenge is that aging continues even during decommissioning. Units 1–6 sustain increasing damage from salt corrosion each day, so it is essential to reconfirm conditions are safe for entry before starting work. To ensure safety, plant staff and partner companies work together, using hammers to tap stairs, ladders, and walkways, checking that they remain secure as decommissioning work progresses.
Salt corrosion is causing increased wear on plant equipment, making pre-start safety inspections vital.
“Of course, we have to pay attention to visible corrosion, but there are other subtle changes we must look out for. For example, once, there was an elevator malfunction. Talks with on-site staff revealed that the elevator had been having issues for several days. We stress the importance of reporting every issue, no matter how small, because minor problems can add up and lead to accidents. Immediate reporting of any concern is emphasized.”
Plant staff frequently engage with on-site workers, distributing salt tablets in summer to prevent heatstroke.
“The most important thing is ensuring that all on-site workers can work safely and confidently—and then return home with a smile,” says Kohata, who regards on-site safety as his highest priority. Each morning, he joins partner company meetings to discuss safety precautions. He balances administrative work with frequent site visits throughout the day to observe conditions and communicate with staff.
Thoughtful Considerations for All On-Site Workers
Considerations for on-site staff are evident throughout Kashima Thermal Power Station. Notable examples include multilingual signs and safety pictograms.
Pictograms are displayed in multiple languages, including English and several Southeast Asian languages.
“In response to the rising number of non-Japanese workers on-site, we initiated these changes at Kashima Thermal Power Station and are now expanding them to other decommissioning sites.”
Monthly safety awards highlight the value of all team members, with Kashima Thermal Power Station recognizing on-site workers who contribute to safety, many of whom are non-Japanese.
Safety award ceremonies are held to recognize the daily efforts of on-site workers and boost motivation.
“When someone goes out of their way to greet others, communicate, or make small contributions, we recognize them. Regardless of nationality or experience, their helmet name is noted, and a lighthearted anecdote is added to their certificate of appreciation. I’ve noticed that non-Japanese employees are often thrilled to receive these and are proud to show them to their families back home.”
Building a Culture Where Everyone Is Treated as Part of the Team
The skills and techniques from Kashima Thermal Power Station are now being applied to decommissioning projects at other plants, including Yokohama Thermal Power Station.
Phase 1 is in progress, with onshore work dismantling chimneys, flue ducts, and the fuel monitoring center for Units 5 and 6, while offshore work dismantles the oil loading pier and cargo wharf.
At Yokohama Thermal Power Station, Units 5 and 6 are being decommissioned, while the advanced combined-cycle Units 7 and 8 remain operational. The priority is strict process management to ensure safe operations without impacting the piping and cables connected to Units 7 and 8. Cross-team communication is essential with different partner companies working in each area.
“As we decommission our plant alongside Kashima Thermal Power Station, I hope we can push each other to do our best,” says Yokohama General Manager Yasunori Eitoku.
“Our visit to Kashima Thermal Power Station gave us valuable insights into their safety practices,” says Yasunori Eitoku, General Manager of Yokohama Thermal Power Station.
“What struck me most was seeing plant staff personally using hammers to check each walkway and staircase, ensuring no one accidentally enters a hazardous area. Rather than relying solely on partner companies, JERA staff at Kashima assume full responsibility for safety management. Their proactive stance provides valuable lessons. At Yokohama Thermal Power Station, we are following Kashima’s example, conducting hammer inspections for structural soundness, clearly marking restricted areas, and establishing designated safe paths. We’ve also introduced safety pictograms for non-Japanese staff. These pictograms, which make it easy to identify hazardous areas at a glance, have proven highly effective.”
While these practices are essential, the most valuable takeaway from Kashima Thermal Power Station has been the mindset of viewing everyone on-site as part of the same team.
During a visit to Kashima Thermal Power Station, he says, “We gained plenty of insights from observing the site and equipment firsthand.”
“Walking around Kashima Thermal Power Station, I frequently see JERA employees actively engaging with on-site staff, and in dangerous situations, they never hesitate to speak up to warn others. Normally, there might be hesitation in cautioning employees from other companies, but here, that commitment to safety is deeply ingrained. At Yokohama Thermal Power Station, different partner companies are responsible for each area, so the cross-communication approach we learned from Kashima is invaluable.”
Yokohama Thermal Power Station emphasizes open communication with partner companies, striving for “a relationship built on open dialogue.”
Sharing Decommissioning Expertise Across Japan
Thermal power plants involved in decommissioning projects are now sharing insights to help tailor strategies for each location. Eitoku, General Manager of Yokohama Thermal Power Station, continues:
“Of course, we conduct site visits to gain firsthand insights through on-site discussions. We also use online tools to share concerns, close-call incidents, and improvements in real time. Since each site has unique conditions, sharing information provides valuable insights—one of JERA’s key strengths, in my view.”
At Yokohama Thermal Power Station, fixed cameras have been installed on-site to monitor safety in real-time (see image 1).
The “Ten Safety Principles” have been established and are being integrated into daily on-site operations (see image 2).
Kashima Thermal Power Station is at the forefront of this field, building expertise daily. Kohata’s enthusiasm shines through when he says, “We strive to pass on the insights and lessons learned here at Kashima to benefit future decommissioning projects at other power plants. We try to actively listen to those on the ground, accurately analyzing issues, proposing solutions, and supporting their implementation.” Kohata’s words reflect his strong sense of responsibility in applying Kashima’s experiences to future projects.
The boiler flue ducts of Units 3 and 4 held sentimental value for the Kashima Thermal Power Station staff. Before dismantling began, everyone gathered for a commemorative photo.
The insights and lessons from Kashima Thermal Power Station extend to other sites, sparking new initiatives. At the start of this article, Watabe expressed his hope that other power plants would adopt “a commitment to stable power supply and an unwavering focus on safety.” He also stressed that daily, consistent communication is essential to make safety the top priority.
“We all have times when we’re tired, and occasional slip-ups are inevitable. What matters most is building a culture where team members look out for one another, checking in on each other and suggesting breaks when someone seems overwhelmed. Safety cannot thrive without a healthy culture, but the workplace naturally improves with one. In decommissioning plants, we hope that prioritizing care for one another and regular communication will lead to zero incidents and accidents.”
“Decommissioning serves as a bridge to ongoing business activities. Everyone here should take pride in this important role,” Watabe encourages the on-site staff.
A power plant’s history is a testament to the dedication of everyone who worked here. There is an undeniable sadness in witnessing the dismantling of something you have dedicated your life to build and maintain. However, this process is also a crucial step in reshaping the site into a new space that meets the needs of the community. That’s why, with a bittersweet appreciation of their memories, each of us must look forward, doing everything in our power to ensure the process is free from accidents and incidents. Our sights are set on a future where new memories can be made.
Following Kashima’s Lead:
Challenges at Chita and Oi Thermal Power Stations
How Two-Way Communication Led to Zero Accidents and Zero Injuries
General Manager, Chita Thermal Power Station
Koji Hondo
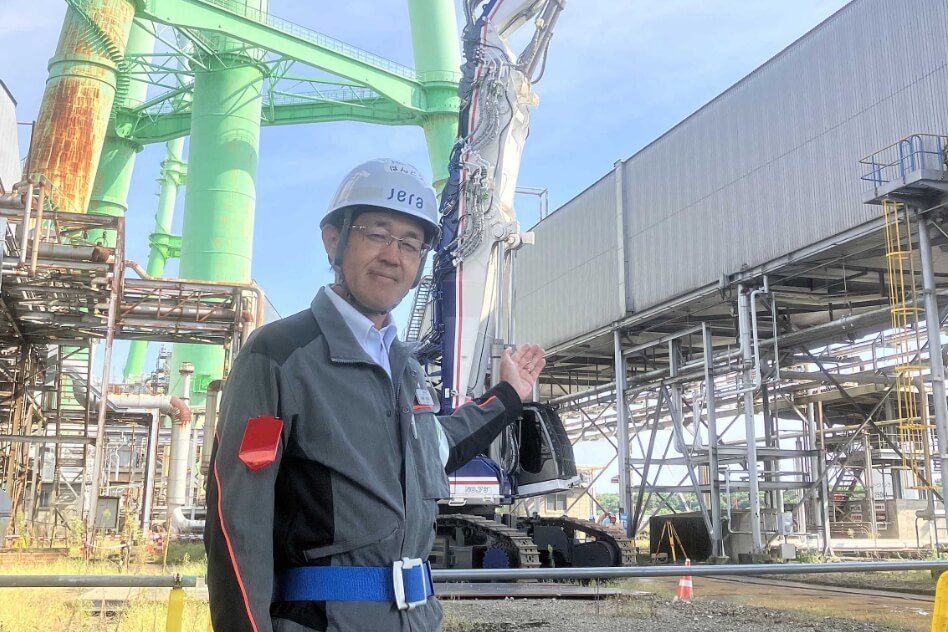
At Chita Thermal Power Station, we are decommissioning Units 1–4 in areas adjacent to Units 5 and 6, which are still operational, with a priority on ensuring zero accidents or disruptions to power generation. During decommissioning, we visited Kashima Thermal Power Station to learn from their firm commitment to safety awareness. Like Kashima, we conduct pre-inspections of hazardous areas and joint patrols with partner companies.
Our top priority for ensuring zero incidents or accidents is fostering "two-way communication." Specifically, this includes (1) accurate communication for mutual understanding, (2) listening to each other's opinions and requests, and (3) ensuring open, equal dialogue between clients and contractors to reach project goals seamlessly. We emphasize these practices in safety meetings with partners and daily briefings, and we are fully committed to zero incidents and accidents. Focusing on team spirit and open communication, we work closely with our partners to advance the decommissioning project.
Toward a Workplace Filled with Laughter, Conversation, and Peace of Mind
General Manager, Oi Office
Rikako Shimagami
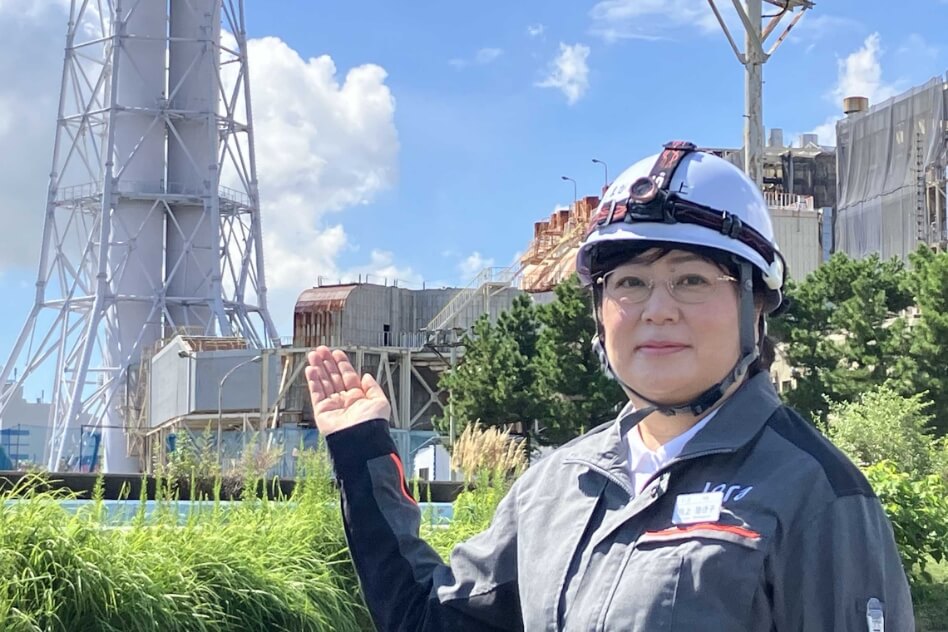
Oi Thermal Power Station is located near expressways, bullet trains, and office and residential buildings, which means we’ve had to adopt measures to reduce our impact on the surrounding environment, which include low-noise methods, such as the jackdown method and rerouting large equipment deliveries to minimize traffic congestion. The project is divided into roughly 60 work units, with preliminary review meetings held to collaboratively address safety, workflow, and potential issues with partner companies. We are also focused on streamlining construction management and creating an information-sharing platform for daily work updates, document exchanges, and other communications with partner companies.
Our approach to supporting on-site staff has been dramatically influenced by lessons from Kashima Thermal Power Station. Learning that many staff members weren't Japanese enabled us to make meaningful improvements, such as providing heatstroke prevention materials and pictograms in several languages. The site is constantly evolving, and we anticipate challenges along the way. However, this decommissioning project relies on the support of nearby businesses and residents. To ensure they feel at ease, we strive to create a workplace filled with “laughter, conversation, and peace of mind” in close collaboration with our partner companies.
RELATED STORIES
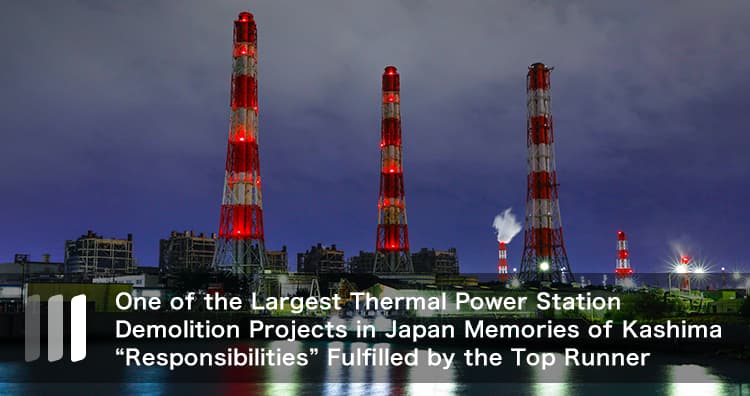
One of the Largest Thermal Power Station Demolition Projects in Japan Memories of Kashima “Responsibilities” Fulfilled by the Top Runner
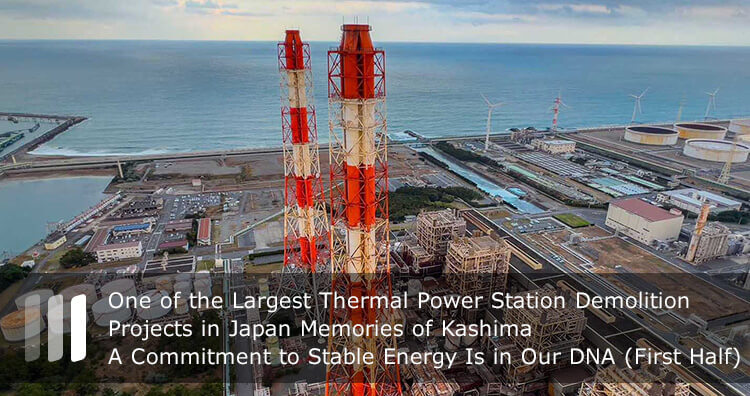
One of the Largest Thermal Power Station Demolition Projects in Japan Memories of Kashima A Commitment to Stable Energy Is in Our DNA (First Half)
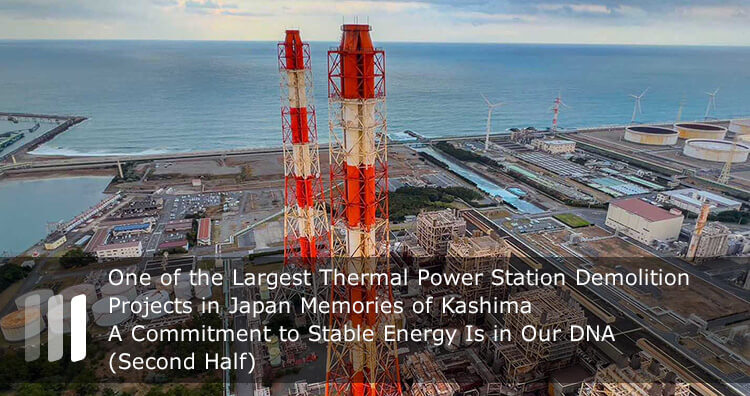